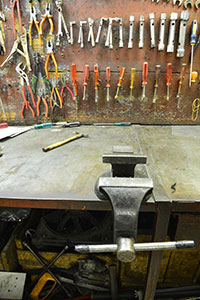
Practicing good housekeeping and organization in a feedyard mechanic shop can not only help save time but may significantly improve overall shop safety.
Identifying feedyard safety principles is one of the aims of Central States Center for Agricultural Safety and Health (CS-CASH). This University of Nebraska Medical Center group (www.unmc.edu/publichealth/feedyard/) is conducting two research projects (funded by National Institutes of Occupational Safety and Health) that are designed to make a positive impact on the sustainability of cattle feedyards through increased safety and health efforts.
“It makes a great deal of sense to keep a shop clean and orderly,” Chuck Pirie, CEO and Content Creation Expert at Safety Made Simple, says. “Often, you have as many as three mechanics working in a shop. If everything is in disarray, you spend time searching for tools and dealing with issues like trip hazards when things lay on the floor. If I see a well-organized mechanic shop, it tells me the person in charge has a similar mindset in regard to their work.”
Some fundamental practices include use of appropriate shelving, storage cabinets and organizers such as bins to help keep tools and products both accessible and orderly. If necessary, build shelves to suit storage needs.
It may work well to use wall brackets or hangers to store hand tools and other items. Pegboards work well for helping keep tools in a convenient location and off the workbench.
All products should be stored in the original container with the label intact. If that isn’t possible, a secure container used to store the product should be clearly labeled with its contents and all label information and instructions. Any flammable products should be stored in an approved fire cabinet.
Fire extinguishers should be accessible within 75 feet or closer if the hazards dictate it. The type and spacing of extinguishers is dependent on the hazards present. A competent vendor of fire extinguishers will help determine the need and also perform the required annual inspections. In addition, all extinguishers should be inspected by feedyard personnel to be certain they have the required charge.
All electrical equipment must be properly grounded, and wiring should include a ground fault circuit interrupter (GFCI) where necessary. Extension cords can short out when driving over them. Heavier extension cords cost more but they are less susceptible to overheating or becoming a fire hazard.
For items that need to be disposed of, don’t allow them to collect from week to week. Follow label disposal instructions for any product that could cause ground or water contamination. Routinely clear out anything that hasn’t been used and isn’t likely to be used in the near future to help avoid accumulating what could become hazardous clutter.
“Quite a few years ago I was on a feedyard when one of the workers was cutting pipe in a Quonset building that doubled as both equipment storage and mechanic shop,” Pirie says. “A front loader and scraper were in the building when he was working with the pipe.”
A used-oil container was also in the building, sitting close to the area where the worker was using a metal cutter. When sparks from the cutting device started flying around the building, it took no time to ignite the used oil container. The worker escaped without injury. However, the building and everything in it was destroyed.
“The fire was so hot that even the metal from the building had to be disposed of, it was so warped from the heat,” Pirie says. “That incident brings home the point that there may be hazards in a shop that have not been addressed in safety training. Just about everyone knows not to stand in a puddle of water when you use electric hand tools. However, anytime you’re ready to start a task in the shop, take 20 seconds to look around. Consider what potential hazards might be around you, and what could go wrong before you start working.”
Routine use of a checklist to review the condition of tools and specific shop areas can be helpful in identifying frayed cords, missing guards, leaks or spills that need to be addressed. However, relying too heavily on a list may result in overlooking a new or emerging issue.
“When a safety poster is put up on the wall, it’s highly visible for two or three weeks. After that it becomes part of the wall and not nearly as noticeable,” Pirie says. “Don’t fall into a checklist mindset. The objective isn’t simply to complete the checklist. You want to consider what’s in front of you, what potential hazards that tool or its location might present. Don’t forget the intent behind use of the checklist, or its not nearly as effective.”
Deteriorating light fixtures or missing/burned-out light bulbs should quickly be replaced or repaired as working with inadequate lighting can lead to many hazards. Newer lighting systems provide outstanding light, may require less maintenance and don’t generate as much heat as older systems.
Damaged or dirty floors can also become a hazard for slips, trips or falls. Shop floor scrubbers, which can quickly do a thorough job, may assist in cleaning floors. Floor repair products are also readily available.
Personal Protective Equipment (PPE) is key to protecting eyes, ears, hands, feet, and lungs when working in a shop. Appropriate footwear includes shoes or boots with a heavy tread and a steel shank or steel toed shoe may be needed, depending on the hazards posed. Earmuffs are easy to put on and take off and can greatly aid in protecting hearing from the loud noises often found in a mechanic shop.
Leather gloves, chemical resistant gloves, hard hats, protective aprons and welding shields are all vital to safely completing tasks such as welding. Goggles with side shields protect against chemical splashes, dust, fumes, and debris from equipment such as bench grinders. A NIOSH-approved respirator (some of which fit under a welding hood) will filter dust, paint fumes, gases or other hazardous material.
Pirie advises that feedyard managers and workers also consider that the mindset of, “accidents only happen to the other guy,” is one of the biggest dangers found in any work setting.
“None of us has to go very far outside our own family to know someone who died due to some kind of accident,” Pirie says. “We can’t control everything that happens in our lives but understanding that we need to do things to help protect ourselves is a big step in working safely. When we’re trained what to do, we need to implement the safety practices we learn.”
Funding for this educational article comes from the Central States Center for Agricultural Safety and Health and the University of Nebraska Medical Center.
Leave a Reply